Today, more and more designers are interested in creating naturally biodegradable materials from organic matters. Such as agar-based biomaterial, which consists of agar powder, glycerol and water. The material can be made by using only kitchen utensils. By adjusting the ratio of the ingredients, and natural additive substances; these edible samples can be created with various textures, colours, opacity, and flexibility. This material has high potential for several applications. However, a lack of appropriate tools made for biomaterials makes it difficult for prototype development.
BioFab 1.0 is a compact and portable working space designed for biomaterial prototyping, from creation to fabrication. It is composed of fundamental tools and utensils which serve different functions for each stage of making.
I imagine BioFab 1.0 as an enabler and facilitator to empower the maker culture community; especially designers, to prototype with new sustainable materials and manufacturing processes.



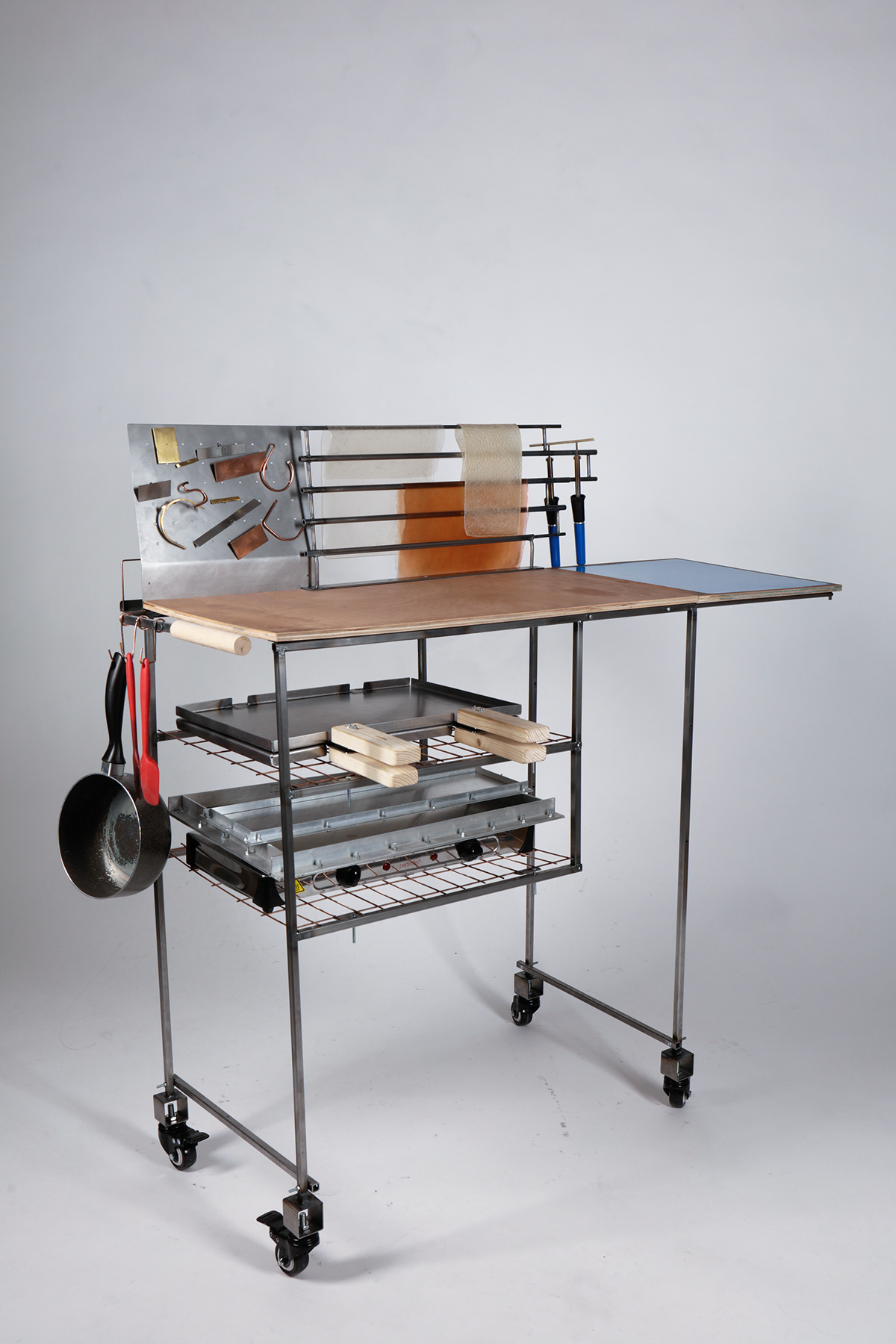


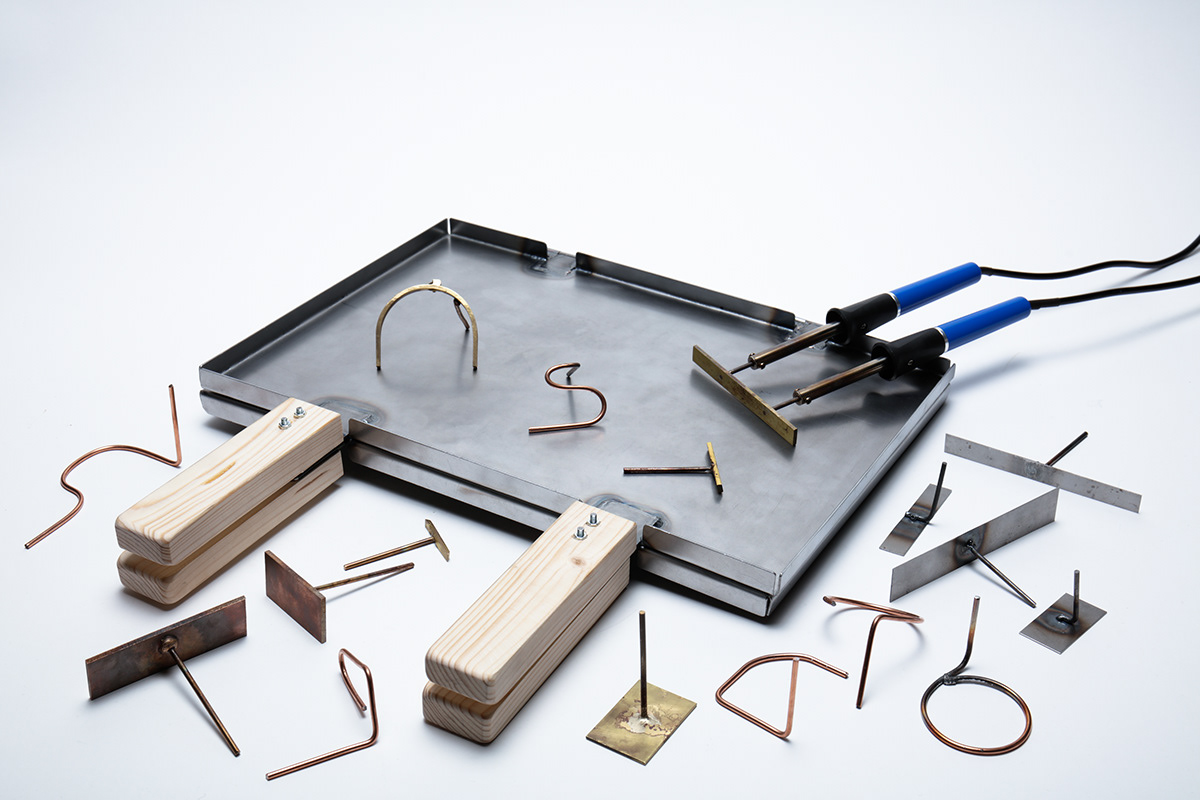
The various surfaces of metal serve the purpose of thermal conduction. When attached to soldering iron, they join sheets together. The biomaterial can be bonded together with heat. It doesn’t require high wattage because its melting point is lower than synthetic materials like plastic or PVC sheet. The shape of the metal can also be customised and personalised based on the design of each project.



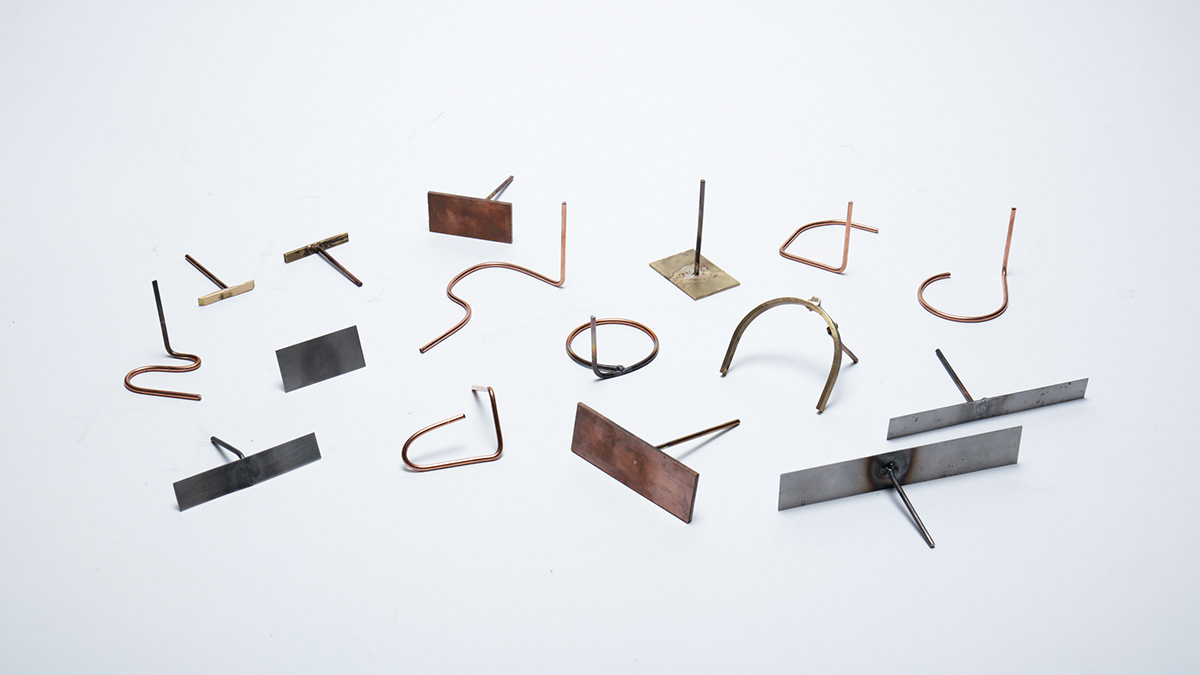


Another tool that works in combination with cheap and readily available heating appliances like a hob is used for joining bigger surface area. You can also layer sheets or offcuts, put other materials between them, and then peel it off later for recycling and composting.

For me, the idea of turning leather-like sheets into a product explores the possibility of it being an alternative to the traditional leather. The process of leather tanning is highly toxic, transforming the leather into a product requires sewing and it’s hard to separate any adhesive or other additional materials when discarded. Meaning my process meets the main criteria for a circular economy principles, unlike traditional leather.
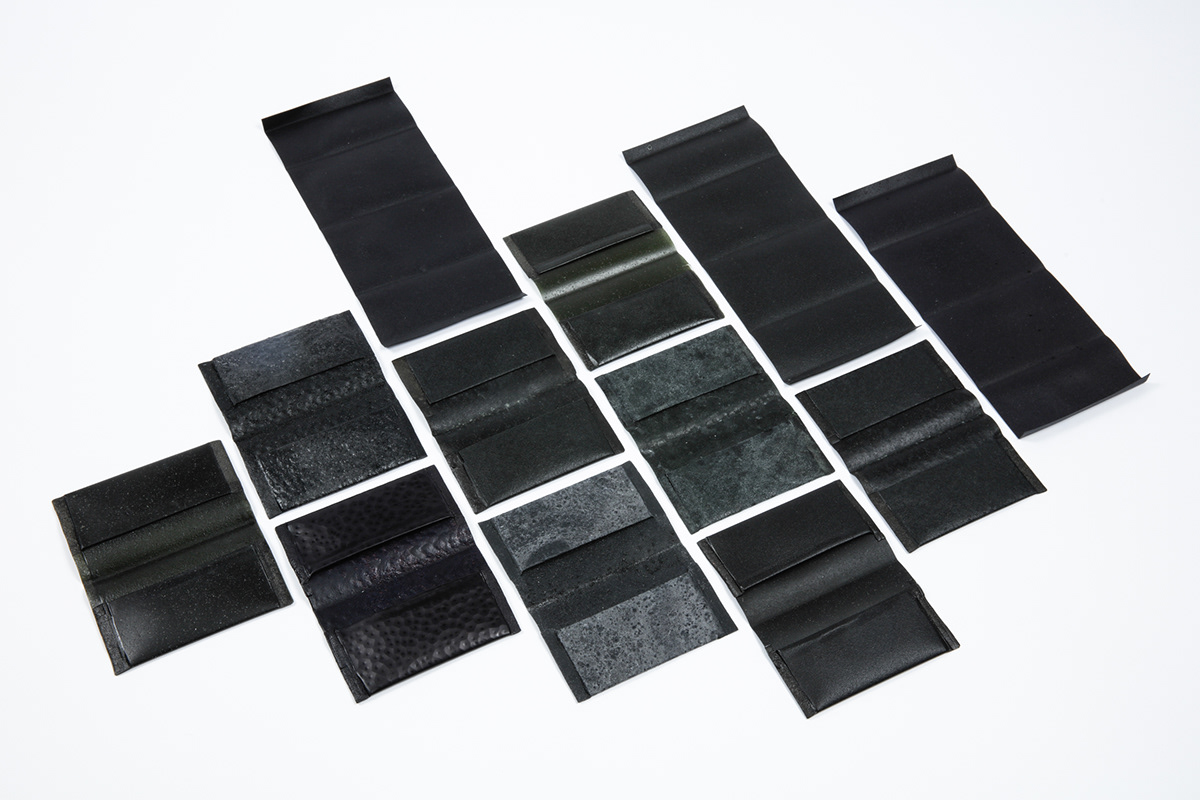



“It’s really helpful that these tools allow me to test similar construction techniques to the sonic welding machine, which is not compatible with non-synthetic materials — I couldn’t achieve this before.” - Hannah Jones (RCA Textiles)
“From a fashion designers perspective, it’s so satisfying to be able to create connections in material without glue, seams or any secondary fibre.” - Søs Hejselbæk (RCA Fashion)
“I’ve been working with silicone but I’m looking for sustainable alternatives, BioFab encourages me to work in a sustainable way without diminishing the original concept of my work.” - Mariana Malta (RCA Fashion)
Coming from different backgrounds, I think we have the power to find a wide range of applications for the material. With the right kind of tools, I believe that we can work together, collaboratively and collectively, towards the sustainable and symbiotic future of manufacturing.


